What is Porosity in Welding: Ideal Practices for Avoiding Permeable Welds
What is Porosity in Welding: Ideal Practices for Avoiding Permeable Welds
Blog Article
The Scientific Research Behind Porosity: A Comprehensive Guide for Welders and Fabricators
Understanding the elaborate systems behind porosity in welding is essential for welders and fabricators pursuing remarkable workmanship. As metalworkers look into the depths of this sensation, they discover a globe controlled by numerous factors that affect the development of these tiny spaces within welds. From the structure of the base products to the details of the welding procedure itself, a wide variety of variables conspire to either intensify or minimize the presence of porosity. In this detailed overview, we will untangle the science behind porosity, discovering its effects on weld high quality and unveiling progressed techniques for its control. Join us on this trip via the microcosm of welding blemishes, where precision fulfills understanding in the pursuit of remarkable welds.
Comprehending Porosity in Welding
FIRST SENTENCE:
Examination of porosity in welding reveals vital understandings right into the honesty and quality of the weld joint. Porosity, defined by the visibility of cavities or voids within the weld metal, is an usual problem in welding procedures. These gaps, otherwise effectively dealt with, can jeopardize the architectural honesty and mechanical properties of the weld, leading to potential failings in the finished product.
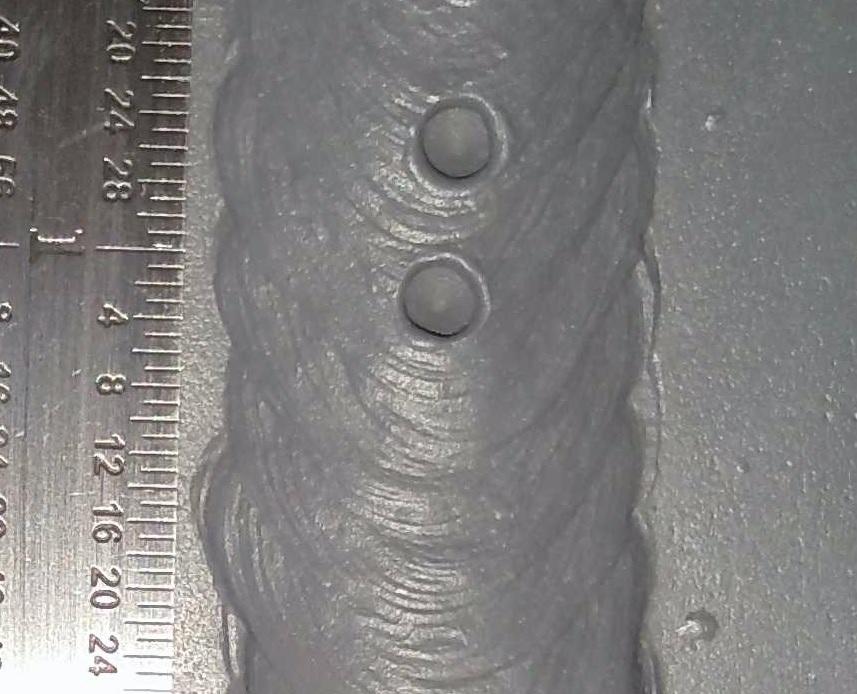
To identify and evaluate porosity, non-destructive screening techniques such as ultrasonic testing or X-ray inspection are frequently used. These methods enable the recognition of interior defects without compromising the stability of the weld. By examining the dimension, form, and circulation of porosity within a weld, welders can make educated decisions to improve their welding processes and achieve sounder weld joints.
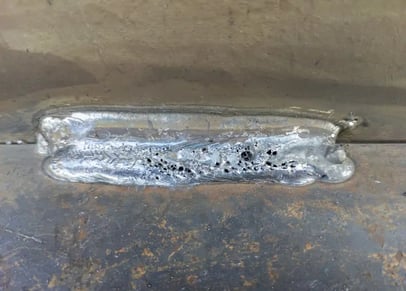
Variables Influencing Porosity Formation
The incident of porosity in welding is influenced by a myriad of aspects, varying from gas securing effectiveness to the complexities of welding criterion setups. Welding parameters, consisting of voltage, existing, travel speed, and electrode kind, additionally impact porosity formation. The welding method used, such as gas steel arc welding (GMAW) or secured metal arc welding (SMAW), can affect porosity formation official source due to variations in warm circulation and gas protection - What is Porosity.
Results of Porosity on Weld Quality
Porosity development considerably endangers the architectural stability and mechanical properties of welded joints. When porosity exists in a weld, it produces voids or dental caries within the product, minimizing the total strength of the joint. These spaces work as stress focus points, making the weld extra vulnerable to splitting and failure under tons. The existence of porosity additionally weakens the weld's resistance to rust, as the caught air or gases within deep spaces can respond with the surrounding setting, resulting in deterioration gradually. Furthermore, porosity can impede the weld's capability to endure pressure or effect, more threatening the total high quality and dependability of the welded structure. In vital applications such as aerospace, vehicle, or architectural constructions, where safety and durability are paramount, the detrimental results of porosity on weld quality can have severe consequences, stressing the value of lessening porosity with proper welding strategies and procedures.
Methods to Minimize Porosity
Additionally, making use of the proper welding parameters, such as the proper voltage, current, and travel rate, is vital in avoiding porosity. Keeping a regular arc size and angle during welding also aids lower the probability of porosity.

Making use of the proper welding method, such as back-stepping or employing a weaving movement, can additionally assist disperse heat evenly and decrease the possibilities of porosity formation. By carrying out these techniques, welders can properly decrease porosity and produce premium bonded joints.

Advanced Solutions for Porosity Control
Applying cutting-edge technologies and innovative visit site methods plays an essential role in achieving remarkable control over porosity in welding procedures. Furthermore, using advanced welding methods such as pulsed MIG welding or customized environment welding can also assist minimize porosity concerns.
Another sophisticated option entails making use of sophisticated welding helpful site tools. Using devices with integrated attributes like waveform control and innovative power resources can enhance weld quality and decrease porosity dangers. The execution of automated welding systems with precise control over criteria can significantly reduce porosity problems.
Additionally, integrating sophisticated tracking and evaluation innovations such as real-time X-ray imaging or automated ultrasonic testing can aid in discovering porosity early in the welding process, enabling immediate corrective activities. On the whole, incorporating these sophisticated remedies can substantially boost porosity control and improve the general quality of welded components.
Verdict
To conclude, comprehending the science behind porosity in welding is important for welders and fabricators to generate high-grade welds. By determining the elements influencing porosity development and carrying out techniques to minimize it, welders can boost the general weld quality. Advanced remedies for porosity control can additionally enhance the welding procedure and make sure a strong and reliable weld. It is very important for welders to constantly educate themselves on porosity and carry out best techniques to accomplish optimal outcomes.
Report this page